Built for Regulated Industries
Proofread Critical
Content at Scale
Drive efficiency across your entire proofreading workflow with the market-leading quality inspection software.
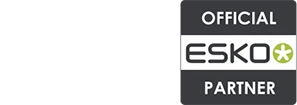
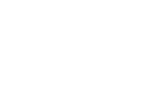
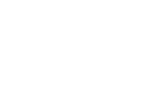
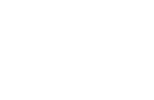

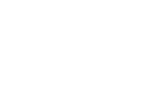
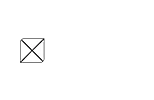
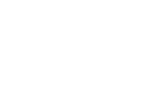
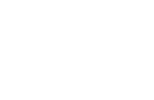

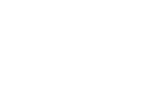
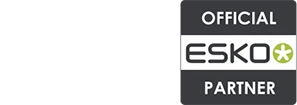
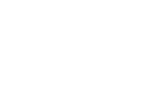
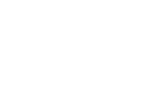
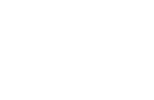

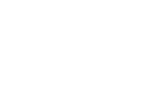
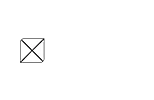
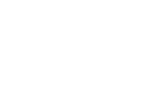
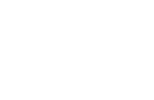

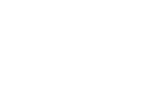
The Trusted Proofreading & Quality Inspection Software for Regulated Industries
Pharmaceuticals, CPG, & Agencies
Regulatory Compliance
Labeling Quality Control
Promotional Materials Quality Control
Incoming Quality Assurance
Print & Packaging
Prepress Quality Control
Production Quality Control
Regulatory Compliance
Ensure file compliance with regulatory guidelines as they move through the review process.
- Automatically inspect text-heavy documents with character-to-character precision
- Quickly identify potential barcode defects and ensure barcode compliance to industry regulations
- Ensure critical text remains compliant as files move across the labeling and packaging process
- Instantly catch spelling errors in 37 languages including your company’s unique terms with Custom Dictionaries
- Inspect thousands of medical terms with a built-in medical dictionary
- Pull files from your AMS or CMS platform and push annotated reports back into it for a seamless quality workflow
- Files Supported
Labeling Quality Control
Run automated file inspections for labeling and packaging to identify discrepancies and errors with complete ease.
- Compare versions with 100% accuracy to ensure only the right changes have been made
- Ensure logos and graphics are accurate and in-line with brand guidelines with pixel-to-pixel graphics inspection
- Instantly catch spelling errors in 37 languages including your company’s unique terms with Custom Dictionaries
- Inspect thousands of medical terms with a built-in medical dictionary
- Ensure barcodes meet industry standards with barcode inspection grading and readings
- Pull files from your AMS or CMS platform and push annotated reports back into it for a seamless quality workflow
- Files Supported
Promotional Materials Quality Control
Reduce the number of content revisions by catching errors early with quick automated inspections for text, graphics, barcode and spelling.
- Compare versions with 100% accuracy to ensure only the right changes have been made
- Generate comprehensive inspection reports to review and navigate through all differences
- Catch spelling errors in seconds with automatic Spellcheck
- Build your own custom dictionaries with terms unique to your organization
- Inspect thousands of medical terms with a built-in medical dictionary
- Inspect text in any language
- Files Supported
Incoming Quality Assurance
Ensure complete compliance of supplier proofs and print-ready files with an all-encompassing quality control inspection.
- Automatically identify all unintended changes in text and graphics before going to print or publishing
- Quickly identify potential barcode defects and ensure barcode compliance to industry regulations
- Inspect colors with delta E accuracy using an exclusive Pantone™ color inspection to ensure compliance with customer guidelines
- Generate comprehensive inspection reports with built-in electronic signatures for an end-to-end seamless approval process
- Files Supported
Prepress Quality Control
Automatically inspect press-ready and imposition files to ensure they’re error-free with GlobalVision’s prepress proofing software.
- Reduce the risk of missed artwork defects by inspecting files with pixel-to-pixel accuracy
- Drive production efficiency by proofing press-ready files in seconds compared to hours
- Prevent wasted materials and excess costs by stopping errors before they’re printed
- Generate comprehensive inspection reports to review and navigate through all found differences
- Ensure barcodes meet industry standards with Barcode Inspection’s grading and readings
- Access GlobalVision’s proofing tools throughout your workflow with the Esko Automation Engine integration
- Files Supported
Production Quality Control
Automatically catch critical errors in print and packaging by verifying printed and digital content against approved files with pixel-to-pixel accuracy.
- Automatically inspect approved prepress files against printed samples with pixel-by-pixel accuracy to identify any critical differences and avoid misprints before going into production
- Ensure barcodes meet industry standards with Barcode Inspection’s grading and readings
- Inspect braille readability and braille dot height to ensure compliance with regulatory requirements
- Inspect colors with an exclusive built-in Pantone color module to ensure compliance with brand guidelines
- Automatically count cartons, inserts, leaflets, and vials with 100% accuracy with GlobalVision’s market-leading automated counting technology, RCount
- Files Supported
The Trusted Proofreading & Quality Inspection Software for Regulated Industries
Pharmaceuticals, CPG, & Agencies
Regulatory Compliance
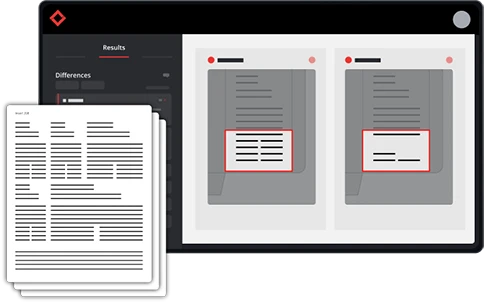
Ensure file compliance with regulatory guidelines as they move through the review process.
- Automatically inspect text-heavy documents with character-to-character precision
- Quickly identify potential barcode defects and ensure barcode compliance to industry regulations
- Ensure critical text remains compliant as files move across the labeling and packaging process
- Instantly catch spelling errors in 37 languages including your company’s unique terms with Custom Dictionaries
- Inspect thousands of medical terms with a built-in medical dictionary
- Pull files from your AMS or CMS platform and push annotated reports back into it for a seamless quality workflow
- Files Supported
Pharmaceuticals, CPG, & Agencies
Labeling Quality Control
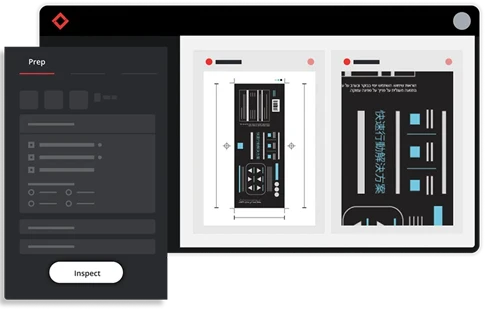
Run automated file inspections for labeling and packaging to identify discrepancies and errors with complete ease.
- Compare versions with 100% accuracy to ensure only the right changes have been made
- Ensure logos and graphics are accurate and in-line with brand guidelines with pixel-to-pixel graphics inspection
- Instantly catch spelling errors in 37 languages including your company’s unique terms with Custom Dictionaries
- Inspect thousands of medical terms with a built-in medical dictionary
- Ensure barcodes meet industry standards with barcode inspection grading and readings
- Pull files from your AMS or CMS platform and push annotated reports back into it for a seamless quality workflow
- Files Supported
Pharmaceuticals, CPG, & Agencies
Promotional Materials Quality Control
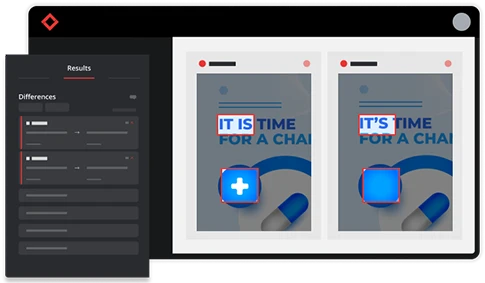
Reduce the number of content revisions by catching errors early with quick automated inspections for text, graphics, barcode and spelling.
- Compare versions with 100% accuracy to ensure only the right changes have been made
- Generate comprehensive inspection reports to review and navigate through all differences
- Catch spelling errors in seconds with automatic Spellcheck
- Build your own custom dictionaries with terms unique to your organization
- Inspect thousands of medical terms with a built-in medical dictionary
- Inspect text in any language
- Files Supported
Pharmaceuticals, CPG, & Agencies
Incoming Quality Assurance
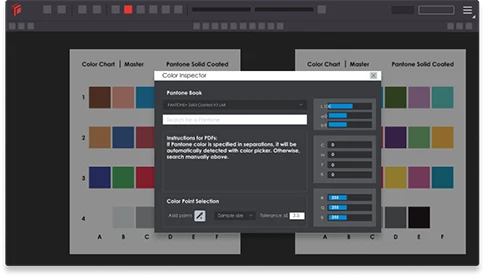
Ensure complete compliance of supplier proofs and print-ready files with an all-encompassing quality control inspection.
- Automatically identify all unintended changes in text and graphics before going to print or publishing
- Quickly identify potential barcode defects and ensure barcode compliance to industry regulations
- Inspect colors with delta E accuracy using an exclusive Pantone™ color inspection to ensure compliance with customer guidelines
- Generate comprehensive inspection reports with built-in electronic signatures for an end-to-end seamless approval process
- Files Supported
Print & Packaging
Prepress Quality Control
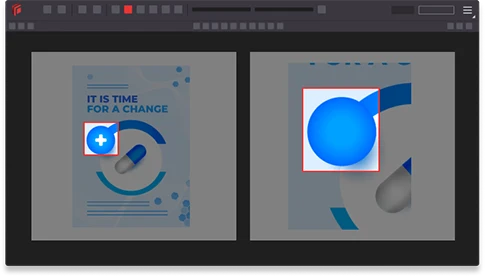
Automatically inspect press-ready and imposition files to ensure they’re error-free with GlobalVision’s prepress proofing software.
- Reduce the risk of missed artwork defects by inspecting files with pixel-to-pixel accuracy
- Drive production efficiency by proofing press-ready files in seconds compared to hours
- Prevent wasted materials and excess costs by stopping errors before they’re printed
- Generate comprehensive inspection reports to review and navigate through all found differences
- Ensure barcodes meet industry standards with Barcode Inspection’s grading and readings
- Access GlobalVision’s proofing tools throughout your workflow with the Esko Automation Engine integration
- Files Supported
Print & Packaging
Production Quality Control
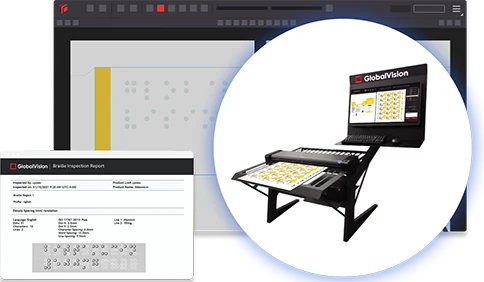
Automatically catch critical errors in print and packaging by verifying printed and digital content against approved files with pixel-to-pixel accuracy.
- Automatically inspect approved prepress files against printed samples with pixel-by-pixel accuracy to identify any critical differences and avoid misprints before going into production
- Ensure barcodes meet industry standards with Barcode Inspection’s grading and readings
- Inspect braille readability and braille dot height to ensure compliance with regulatory requirements
- Inspect colors with an exclusive built-in Pantone color module to ensure compliance with brand guidelines
- Automatically count cartons, inserts, leaflets, and vials with 100% accuracy with GlobalVision’s market-leading automated counting technology, RCount
- Files Supported
Switching to GlobalVision Gets Results
%
81% of pharma executives are accelerating the review process through automation
%
100% accuracy in proofreading, according to a GlobalVision G2 Review
10x faster than the average proofreading software
%
33% decrease in proofreading and review times, according to Pfizer
Identify and Eliminate Errors;
Even the Smallest Discrepancies
From file creation to print, GlobalVision pinpoints exact differences and errors in text and artwork with pixel-to-pixel accuracy.
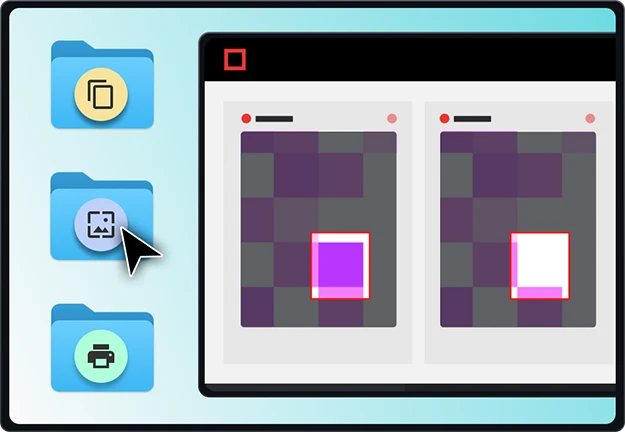
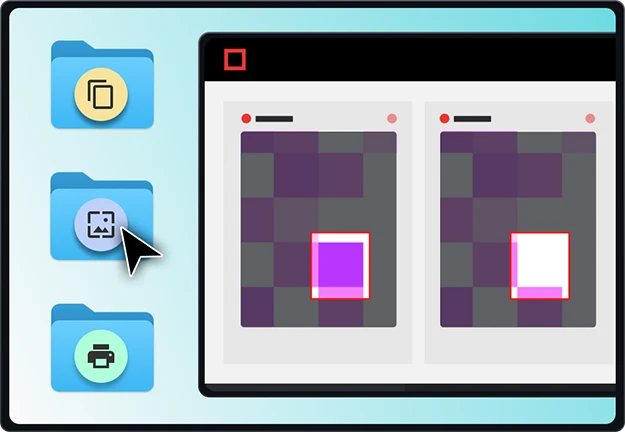
Identify and Eliminate Errors;
Even the Smallest Discrepancies
From file creation to print, GlobalVision pinpoints exact differences and errors in text and artwork with pixel-to-pixel accuracy.
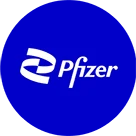
“GlobalVision has allowed us to have an integrated system that is technologically advanced and sophisticated allowing for fast analysis. At the same time, the system is extremely user friendly and the support and training provided by GlobalVision made the transition process seamless.”
Veronica Guilliams
Senior Manager – Visual Inspection at Pfizer
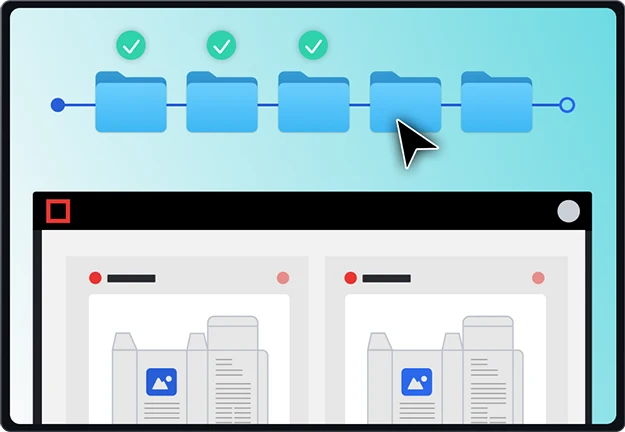
Drive Efficiency Across the Entire Quality Inspection & Review Workflow
Eliminate the hours spent searching documents for errors. Get your products to market in record time without compromising quality by removing time-consuming and error-prone manual checks.
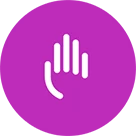
“GlobalVision software provides accuracy and minimizes the number of people reviewing documents. This saves time and allows us to commit to shorter turn-around timeframes.”
Jan Meyers
Global Labeling Sr. Specialist, Regulatory Affairs at Bristol Myers Squibb
Mitigate Risk
& Maintain Compliance
Reduce the risk of costly reprints and recalls, while also ensuring files maintain compliance with regulatory requirements as they move through the review process.
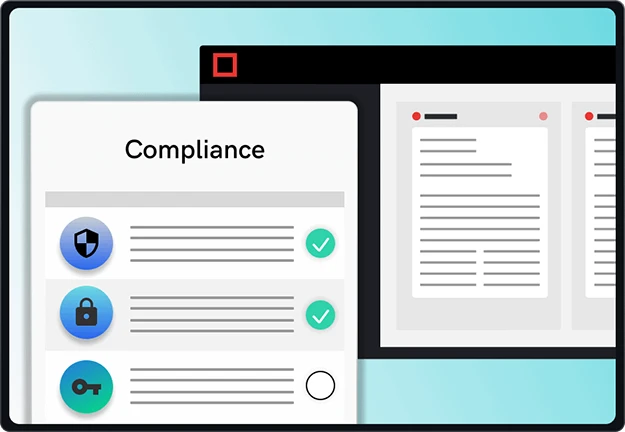
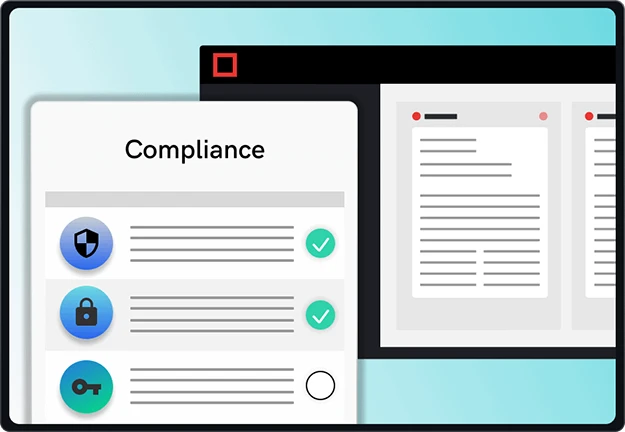
Mitigate Risk
& Maintain Compliance
Reduce the risk of costly reprints and recalls, while also ensuring files maintain compliance with regulatory requirements as they move through the review process.
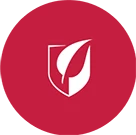
“Business problems and benefits realized are the same — increased accuracy in quality checks of artwork preparation, reduced amount of human error in the proofreading process, and reduced amount of time in performing the quality checks.”
William Bosley
Manager Global Labeling and Graphics at Gilead Sciences
The Only Proofreading Solution You Need to Scale
Hear first-hand how GlobalVision has provided customers with complete confidence in the proofreading and quality control workflow
Decades of successfully streamlined and efficient workflows have resulted in consistently accurate and efficient packaging and labeling, proving GlobalVision a key component in J&J’s quality mandate.
To ensure their products’ quality, accuracy, and consistency, Smurfit Kappa MNL in the Netherlands turned to GlobalVision as the solution to their inspection and verification problems.
See how GlobalVision’s become a key component in J&J’s quality mandate through successfully streamlined and efficient workflows.
See how Smurfit Kappa MNL in the Netherlands found the solution to their inspection and verification challenges with GlobalVision.