How to Effectively Manage Print Samples with Automation
Date: August, 2021 | Category: Quality | Author: Kayla Caticchio
Our world is growing at a rapid pace and so is the consumer market. The space between the market and the consumer’s home has drastically shrunk in recent times, with online marketplaces quickly replacing traditional shopping experiences. Consumers now have access to products from all over the world – and they can get them delivered directly to their homes with minimal effort.
With so much competition between brands, packaging design is a key way to distinguish your company from others and thus persuade consumers to purchase your products. That is why brands must take great care to avoid little errors that can ruin a great packaging design.
What Errors Can Ruin Great Packaging Design?
The opportunity for errors to be created increases as text and artwork files are converted into prepress files.
They can become distorted and prone to critical errors. Consequently, print errors can also occur during production.
Examples of these errors include text errors like missing or dropped text, inserted or deleted words, and font errors. Graphic errors like misregistration or artwork deviations can also occur. Spelling errors are also common, especially when adapting packaging components into foreign languages for use in overseas markets.
Problem with Manual Sample Inspections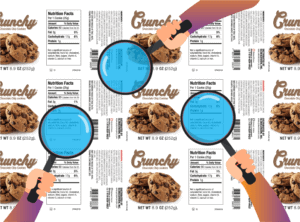
Brands don’t have to cut corners to save time when it comes to proofing print samples. Companies that outsource printing understand the importance of checking packaging components once they’re completed and sent back from the print supplier.
It’s unrealistic to expect companies to visually inspect every single printed component, especially given the cost of resources and labor involved. That’s where sampling comes in. With sampling, the quality control department will determine the number of copies they must check to reasonably conclude that the entire shipment can be approved. For example, only 40 copies will be proofread out of thousands.
The problem with manually inspecting small sample sizes is that defects could be localized elsewhere and might be missed by the proofreader. Clients should always be aware that the printers they deal with likely have other customers and complete many jobs daily. Gang runs, during which different products are printed on one sheet to reduce waste and save money are a regular occurrence. As a result, mix-ups can commonly occur.
Artwork Automation for Print Samples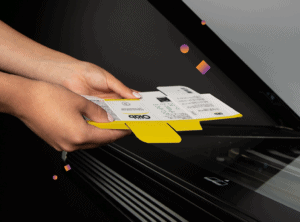
Automated quality control like GlobalVision helps both printers and incoming quality assurance departments ensure that printed samples are free from critical errors. For brand companies, automated quality control tools allow them to compare physical copies to the approved artwork that was originally sent to the printer. Quality control departments simply have to scan the selected physical samples to then compare them back to the original artwork file.
The problem with manually inspecting small sample sizes is that defects could be localized elsewhere and might be missed by the proofreader. Clients should always be aware that the printers they deal with likely have other customers and complete many jobs daily. Gang runs, during which different products are printed on one sheet to reduce waste and save money are a regular occurrence. As a result, mix-ups can commonly occur.
The Benefits of Automated Artwork Inspections
- Brands can keep track of version changes while ensuring that the right content was printed.
- Multiple production samples from various print suppliers can easily be managed.
- Brands can protect themselves from both financial and raw materials loss by ensuring work has been printed properly.
- Errors in text, artwork, spelling, barcode, and more can be detected in seconds versus hours.
Automating the process of checking printed samples has many benefits for companies that need to get their products to market quickly. Aside from the time and cost savings, ensuring that products make it to the consumers in packaging that is entirely error-free is crucial. By replacing the manual inspection of samples, businesses have more resources available to focus on R&D and other projects.
———————————————————————————————————————————————————
- To learn more about GlobalVision’s automated quality control tools, click here.
- Ensure your content is always error-free in record time with GlobalVision. Try it now for free.
- Keep up with the latest updates in automated quality control. Sign up for our newsletter.